Introduzione
A common technique for creating high-end plastic components with improved physical characteristics, such as tensile strength, heat resistance, and corrosion resistance, is modified nylon injection molding. The formation of bubbles is one of the frequent issues that arise in this procedure, though. These bubbles can degrade the completed product’s quality by introducing cosmetic flaws and decreasing its structural integrity. Therefore, it is crucial to understand how to avoid and deal with bubbles when using modified nylon injection molding.
Bubbles in Modified Nylon Injection Moulding: Causes and Solutions
Understanding the underlying causes of bubbles in modified nylon injection molding is essential before considering solutions. Some of the elements that might cause bubbles to occur during the injection molding process include the following:
1. Insufficient Nylon Drying
Inadequate drying of nylon pellets is one of the main reasons of bubbles in modified nylon injection molding. Due to its hygroscopic nature, nylon tends to absorb moisture from its surroundings. During the molding process, bubbles may form as a result of moisture in the nylon pellets.
2. Variable Melt Temperature
During the injection molding process, the melt temperature of the nylon material is crucial. If the temperature is too low, bubbles may occur in the plastic when it solidifies too rapidly. However, if the temperature is too high, nylon may begin to break down, which also results in bubbles.
3. Bad Ventilation
Allowing air to escape from the injection mold cavity while molding is a technique known as venting. Inadequate venting can trap air inside the mold chamber, which can cause bubbles to develop.
4. Rapid Injection Rates
High injection speeds may result in bubble formation in the mold cavity due to turbulence.
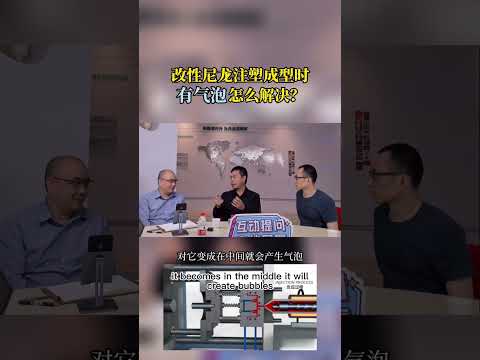
Solutions for Modified Nylon Injection Moulding Bubbles
1. Proper Nylon drying
It is crucial to make sure that the nylon pellets are sufficiently dried before the injection molding process in order to prevent the production of bubbles. The optimum range for drying temperature and drying time for pellets is between 80°C and 105°C.
2. Reliably Low Melt Temperature
It’s crucial to maintain a constant melt temperature throughout the injection molding process. For nylon, a melt temperature of between 260°C and 305°C is advised. In order to prevent overheating or underheating of the nylon material, the temperature should be regularly checked.
3. Sufficient Venting
To stop bubbles from forming, the mould cavity must be properly vented. To guarantee that the air can escape during the molding process, this may be accomplished by constructing the mould with sufficient vents or by installing a venting system.
4. Sluggish Injection Rates
By decreasing turbulence inside the mold cavity, using a slow injection speed can aid in preventing bubble formation. The size and intricacy of the moulded item should be taken into consideration while adjusting the injection speed.
Conclusione
The quality of the final product can be significantly impacted by bubbles in modified nylon injection molding. It is possible to stop bubbles from forming and enhance the quality of the finished product by addressing the underlying causes of bubbles and putting the right solutions in place. One of the best strategies to stop bubbles from forming during modified nylon injection molding is to dry the nylon properly, maintain a constant melt temperature, provide appropriate venting, and use modest injection rates.